The best quality porcelain wall and floor tiles in the world are crafted in Europe, principally in Italy and Spain. Each design from Lapicida has been carefully chosen from the best of those European manufacturers. They trust Lapicida to offer their designs on an exclusive basis.
Lapicida has decades of experience with stone and marble. Technological advances now mean that the best European porcelain tiles are simply too good to ignore, which is why we have embraced them alongside our renowned stone and marble offerings. Porcelain should be viewed as a surface in its own right, with its own place in the market alongside stone and marble. Indeed, porcelain has many advantages over natural stone being, for example, resistant to chemicals in swimming pools and to rock salt on exterior terraces, whilst also having inherent anti-bacterial qualities. No longer should the best porcelain tiles be considered a “poor man’s substitute” for natural surfaces. Quality European porcelain tiles are now virtually indistinguishable from their natural equivalent as the artisan producers we choose have decades, sometimes centuries, of expertise from the precise mix of clays and minerals through to the correct firing to exacting standards.
Whilst porcelain tiles are man-made, they recreate the look and texture of their natural equivalents and are created using similar techniques. Whilst natural stones and marbles are the result of millions of years of compaction and heat, their porcelain equivalents are created in a fraction of that time using 50,000 tonne presses before being heated to just over 1200 degrees Celsius. Below is a more detailed look at this highly-sophisticated production process.
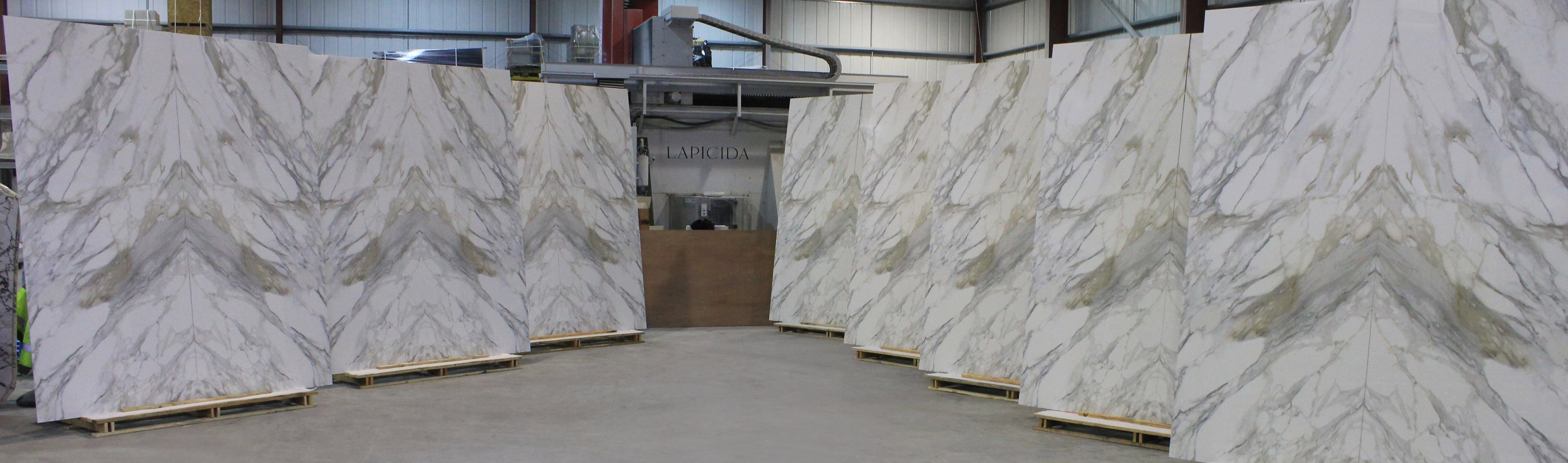
How are porcelain tiles made?
Porcelain tiles today can be seen as the modern successor to historic terracotta tiles which were entirely man-made, with clay being compacted into moulds using simple tools and human strength before being fired using rudimentary kilns.
Porcelain tile manufacture is now a much more sophisticated undertaking, although still made from natural materials, typically including kaolin clay, feldspar and quartz. These natural materials are mixed together with water for up to 8 hours in huge drums, before forming balls and being removed ready to be pressed to the correct thickness.
Multiple presses are used to create multiple surface textures, finishes and sizes – making stone and wood effect porcelain tiles extremely realistic when installed as this avoids unnecessary pattern repeats. Indeed, each porcelain style typically includes up to 20 or more different surface patterns. This means that each finished floor or wall surface in a project takes on its own unique character, just like their natural equivalents.
A state-of-the-art printer is used to apply the desired colour and glaze to the surface. This advanced printing technology allows for precise and intricate designs that accurately replicate natural surfaces. This technology has truly transformed ceramic and porcelain tiles, making the best quality tiles very difficult to distinguish from the genuine material they replicate. Not only has it made possible more realistic reproductions of other surface materials, those reproductions also feel real to the touch as the printing process includes texture, right up to the edge of the tile, even when distressed.
The pressed and printed porcelain is baked in a kiln, initially at a temperature of 300°C. The heat then rises to 1240°C before lowering again to 300°C all within a firing cycle of around four hours. When fired correctly, these the raw materials fuse uniformly and create an incredibly dense tile with porosity of around 0.05%. This means the tiles meet ISO and other international standards, whilst also being highly resistant to staining and benefitting from long-term, low maintenance requirements.
After firing the tiles are stored in huge racks to cure before being subjected to rigorous quality control including the scanning of every tile for any cracks, fissures or other production defects. Anything less than perfect is rejected.
A top quality porcelain manufactory is a massive investment as much of the operation is automated. This is a huge entry barrier for any competitors in other countries and explains why some products fall short of high quality demanded by knowledgeable private clients and professional designers.
When comparing porcelain and ceramic tiles, although the terms have almost become interchangeable, the key technical difference is that porcelain is fired at higher temperatures and greater pressures than ceramic tiles. This reduces voids and cavities in the porcelain tile, typically making them less porous and stronger than their ceramic equivalents, providing extra durability in the long term.
Why consider porcelain tiles?
Porcelain tiles do not contain plastic, are not flammable and do not release toxic fumes. They do not expand, deform or deteriorate, are bacteria resistant and, when correctly installed, guarantee a long-lasting, hygienic surface in every room of a house, workplace or hospitality venue.
Porcelain tiles offer countless stylistic solutions for designers and private clients as they are incredibly versatile, ideal on floors and walls, countertops and tables, and available in many sizes and surface finishes.
Tiles made from porcelain can be viewed as having a low carbon footprint as they can be transported efficiently and, once installed, are both hard wearing and long lasting. And, at the end of their life, they can either be recycled or can be considered inert waste.
ARTIS is the name given to Lapicida’s exciting collection of next-generation porcelain - replicating natural stone, marble and wood. Lapicida offers unique, yet affordable, ranges of top-quality porcelain tiles that are always in stock for immediate dispatch. Large format tiles are a speciality. With Lapicida, you can realise your dreams at affordable prices - from just £39/m2.